The work piece is fixed by the splice tray and the spindle and the motor drives the spindle to rotate. The pendulum frame detects unbalanced amount and then passes through the triangular chuck clamping plate, turns to the positioning, The positioning clamping system is one of the most critical parts in fully automatically balancing machine in which the positioning of the three-jaw chuck on the work piece is achieved by direct clamping of the adapter plate.
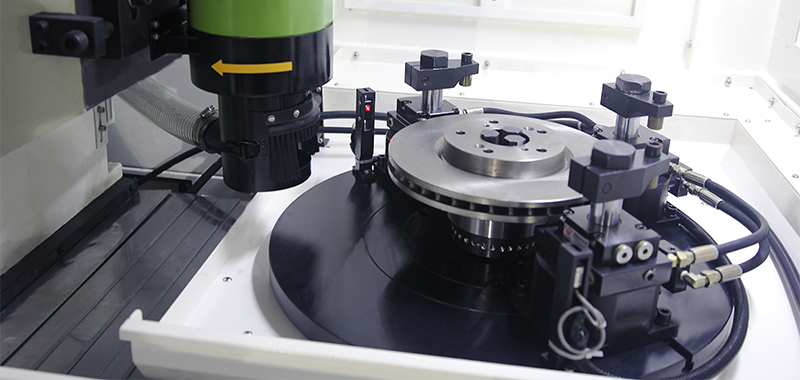
Three-jaw chuck can damage to balancing machines’ spindle:
1. Three-jaw chuck generates larger radial force on the body of the three radially moveable claws. This larger clamping force go access through chuck to the spindle.
2. A long time damage, the chuck wear and three claws will appear bells shape breaches.
3. The chuck will gradually deviate out of the spindle due to processing and wear
4. Spindle flange is solid structure.
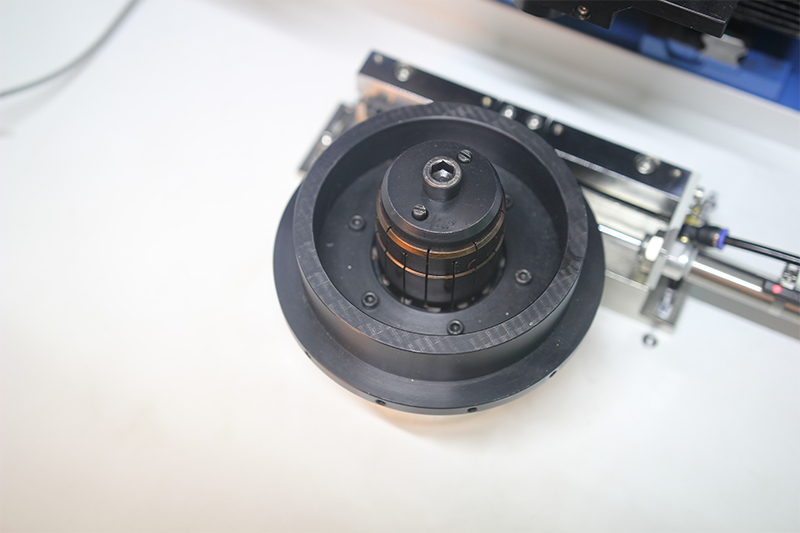
There are several reasons that can cause the radial force to the spindle when the spindle splice is clamped. The spindle is one of the most important components of the automatic balancing machine. The spindle sleeve installation is more complex and the spindle is not easy to replace. In order to overcome the damage, we use a new retractable spindle splice device that eliminates chuck clamping the damage to the spindle, and will not affect the spindle drive work piece on the measurement of unbalance, which is generally applied to the disc rotor vertical automatic balancing machine positioning.