1. Causes of crankshaft unbalance:
(1). Special structure of the crankshaft
The connecting rod is mounted on the connecting rod journal of the crankshaft, and the center of connecting rod journal and the main journal have certain distance. Due to the above two journals are not concentric, when the crankshaft rotates, the inertial masses of the piston and the connecting rod cause the crankshaft losing its balance, and then generating a large unbalanced force (i.e., centrifugal force). This unbalanced force will increase the load on the main journal.
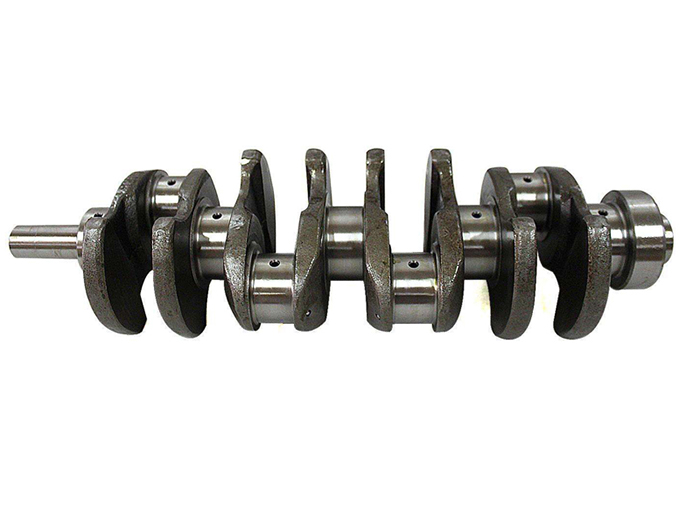
In order to eliminate this unbalanced force, the balance block need to be installed on the crankshaft to reach balance. The mass, size, shape and installation position of the balance block should be designed reasonably to overcome the centrifugal force generated in the crankshaft rotation and reduce the load on main journal.
(2). High-speed rotating working environment
The crankshaft rotates at high speed, workpiece with high speed should satisfy static and dynamic balance both. So all high-speed rotating parts need to be balanced, such as flywheels, drive shafts, clutch pressure plate etc.
The purpose of balancing was to decrease the vibration amplitude and frequency of the crankshaft when it rotates at high speed. If unbalanced, it will generate a momentum peak, and even can lead to the crankshaft fracture.
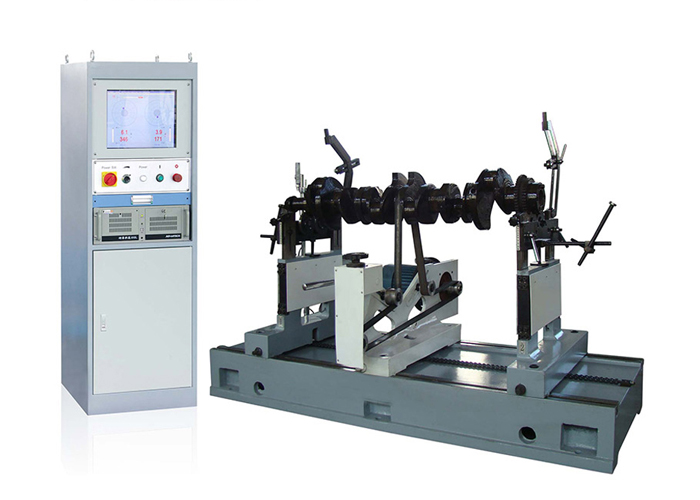
2. Application of crankshaft dynamic balance
Crankshaft is a special type of rotor, it does not have a correction plane at any position for structural reasons. That is to say, we can't find an entire circumferential plane to do correction, no matter where the correction plane is. And adding weight (or removing weight) operation which aimed to improve balancing situation can only be done at certain special locations. In addition, crankshaft was multi-point support when working, and its working speed was far below the critical speed, so the crankshaft can be regarded as a kind of rigid rotor with special structure.
Generally, it was tested by dynamic balancing machine, and then remove some materials in the unstressed part of the crankshaft to reach balance.
The dynamic balancing machine corrects the unbalance amount of the rotor based on the measured data, and can improve the mass distribution of the rotor with respect to the axis, so that the vibration generated when the rotor rotates or the vibration force acting on the bearing is reduced to an allowable range. Therefore, the balancing machine is an indispensable device for reducing vibration, improving performance and upgrading quality.
Usually, rotor balance includes unbalance measurement and correction two steps. The balancing machine is mainly used for the measurement of unbalance, and the correction of unbalance is usually done by other auxiliary equipment such as drilling machine, milling machine and spot welder, or by manual method. Some balancing machines have made the correction device a part of the balancing machine.