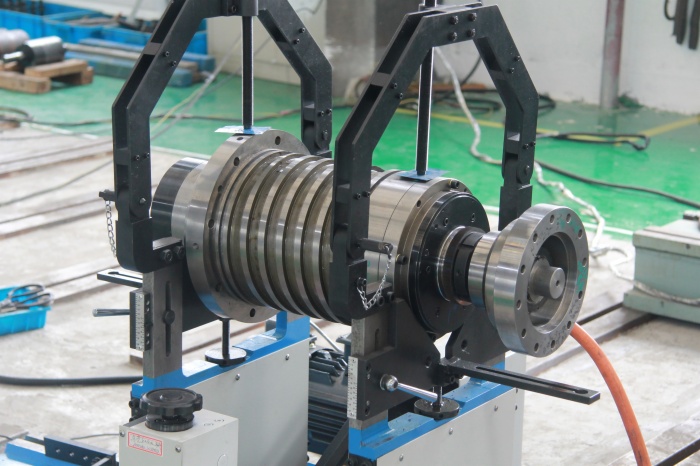
The purpose of the spindle balance is mainly determined by the machine characteristics and machining accuracy. Any type of spindle or its components must be balanced before the balance to determine the level of accuracy. For some machine tools, the balance is a process of spindle production. The dynamic balance through the spindle vibration, bearing vibration or bearing reaction has reduced to a certain range. Balancing the spindle is not only on the balancing device but also in working conditions. Therefore, we must strictly abide by the provisions of dynamic balance standards to ensure the balance of shaft accuracy. The dynamic balance of the rigid rotor standard provides that the accuracy of the rotation axis level is mainly for the balance body, such as the spindle or its components. According to the production situation, the spindle, rotor, fan, nut and other parts combine a spindle, and then move the balance. The unbalanced vibration of the machine tool spindle is affected by many factors. In addition to the spindle itself, such as the quality of the machine body and the foundation, the stiffness of the bearing, the speed of operation and the resonance frequency are close to the damping. Therefore, a machine tool spindle dynamic balance, the size of the remaining unbalance to determine the size has to consider a variety of factors.
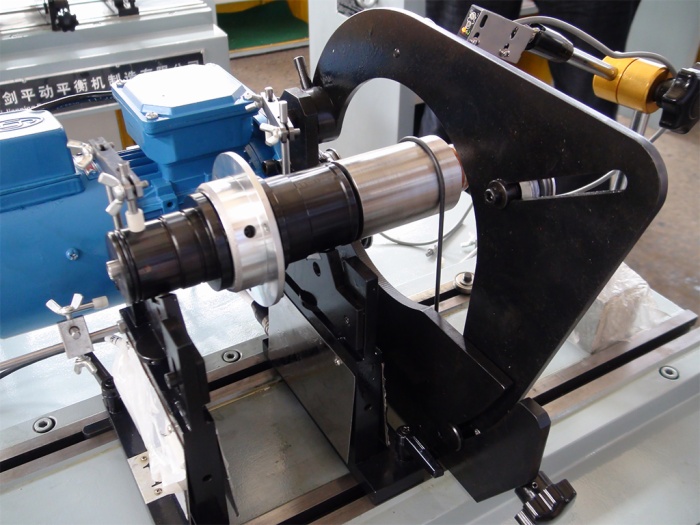
Since each spindle always has a certain initial imbalance. It is first necessary to estimate the initial unbalance of the shaft. When the initial unbalance value exceeds a certain value, if the two calibration plane balance is in the high-speed range of operation, it may not be a reliable balance. Therefore, the initial unbalance amount is controlled in the design, manufacture and assembly of the spindle by calculating a limit value for each type of shaft in advance, thereby limiting it to this.