Dynamic imbalance is a very common imbalance, which is a combination of static imbalance and even imbalance.
After the unbalanced rotor is corrected by dynamic balance, it not only eliminates the even imbalance, but also eliminates the static imbalance. At this time, the central inertia main axis and the rotation axis of the rotor are completely identical, and the rotor is balanced. But the ideal is that the fullness of the reality is bone-like. It is impossible to balance an unbalanced rotor to an unbalanced amount of zero. Because of the accuracy of the dynamic balancing equipment and the limitations of the rotor. Therefore, there is a concept of balance accuracy, that is, a reasonable numerical magnitude that we can achieve under the existing conditions, thus satisfying the requirements of production and life and meeting the economic requirements.
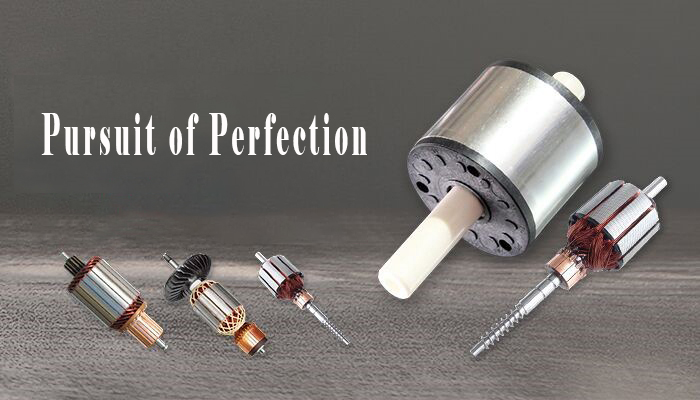
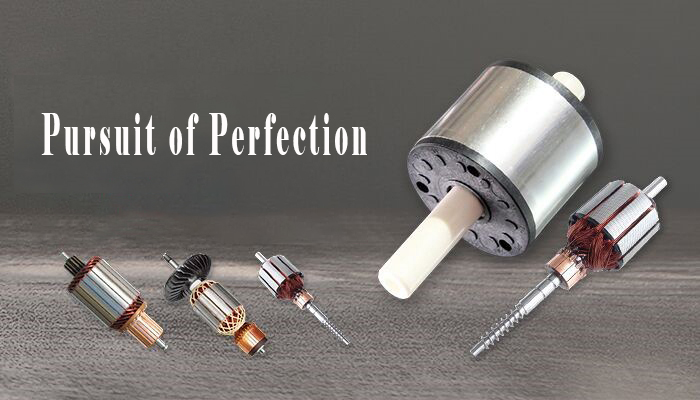
what circumstances do you want to check the balance?
During the assembly process, the gap created between the various components conforms to the installation standard but for the entire rotor component, its cumulative error may exceed the dynamic balance accuracy of the rotor. In particular, for some rotor parts with bearing bushings, it should be checked by dynamic balance before final assembly.
Accuracy requirements for dynamic balancing machines
The hard-bearing balancer can be directly expressed in small residual unbalance on the calibration surface in grams (mm/mm) and some in grams/cm.
The small reachable residual unbalance is affected by factors such as the type of the balancing machine, the measuring method, the transmission mode, the bearing form and the plane separation ratio of the correction surface, and the sensitivity of the balancing machine.
To make the balance accuracy of the rotor high (that is, the amount of residual imbalance is small), it is necessary to eliminate the factors that affect the accuracy of the imbalance. Among these influencing factors, the transmission mode of the balancing machine and the imbalance of the transmission parts have a great influence. The journal accuracy of the rotor should also be strictly limited. There is also a rotor member with an impeller, a rotor whose center of gravity is not at the center of the rotor, a bearing bottom sleeve and a rotor that seals the packing.
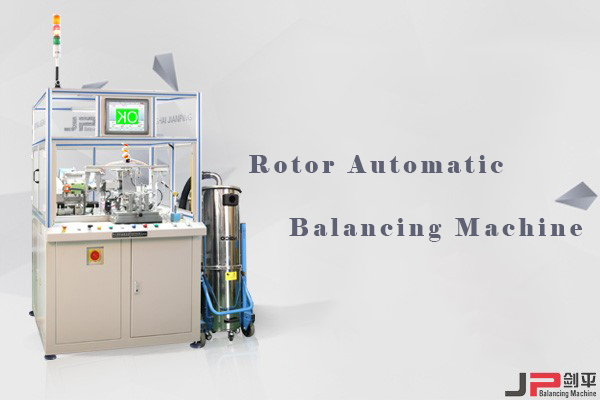
Rotor automatic balance machine - rotor dynamic balance process and method
For rotors with a large initial imbalance and excessive vibration during rotation, a one-sided balance must be performed before dynamic balance verification to eliminate static imbalance. Sometimes due to improper selection of the correction surface position (ie, the center of gravity is not within the selected correction plane), correcting the static balance will increase the even imbalance. Therefore, the correction surface is selected to be performed in the plane of the center of gravity to reduce the even imbalance. If the plane of gravity is not allowed to be de-duplicated, it should generally be performed on two planes on both sides of the plane where the center of gravity lies.
In order to reduce the time and labor involved in the balancing operation, efforts should be made to reduce the amount of correction. For this reason, after the dynamic balance measurement of the rotor of the balancing machine, the rotor can be weighted and de-emphasized as needed. Balanced machining of the rotor by the method: The so-called weighting method, that is, correcting the weight in the opposite direction of the imbalance. The de-weighting method removes a certain weight in the unbalanced direction. Commonly used methods are: boring, drilling, chiseling, milling, grinding, etc.
The Shanghai Jianping Rotor automatic balancing machine can solve the rotor imbalance problem very well. The de-weighting dynamic balance processing method can be used to balance and correct the rotor with a weight of 0.5 kg and a diameter of 40 mm. As a balancing machine manufacturer, Shanghai Jianping also manufactures various types of rotor balancing machines to achieve a better balance of the rotor.